Which material should I choose for my print?
- paulforce
- Sep 24, 2020
- 5 min read
Updated: Sep 28, 2020
Choosing a material to print with depends on many factors, such as material costs, availability and material characteristics. It also depends on what the end component is going to be used for.

For example for rapid prototyping PLA allows for quick iterative designing, while reducing material costs but with little part strength. PLA is also offered in a variety of colours, typically used for first iteration prototypes.
PLA is by far the easiest material to print with, and is available in a variety of colours and textures such as wood and glow in the dark. However PLA should not be used for objects used outdoors that are exposed to direct sunlight.
(PLA PART)
Some 3D printing materials need to be food grade or medical grade, PETG is an example filament material that can come in medical or food grade variants. The cost of PETG is slightly more expensive than PLA, however the strength and durability of PETG is much higher than PLA. PETG is less brittle compared to PLA and therefore a bit more forgiving when flexed. PETG is available in a variety of colours.
(PETG PART)
For aerospace and automotive applications part strength is key, filaments such as Carbon Filled Nylon offer high strength and durability. The Nylon is reinforced with chopped Carbon Fibres, providing light but incredibly stiff components. The cost of high grade materials such as CF Nylon is higher than PETG or PLA.
(CF Nylon PART)
Some parts or products require flexibility or a rubber like feel, TPU is a fantastic filament that produces parts with some flex such as soft phone cases. TPU is more durable than PLA and PETG while not being brittle. The cost of TPU is similar to that of PETG. TPU is available in a variety of colours.
Material Characteristics Comparison
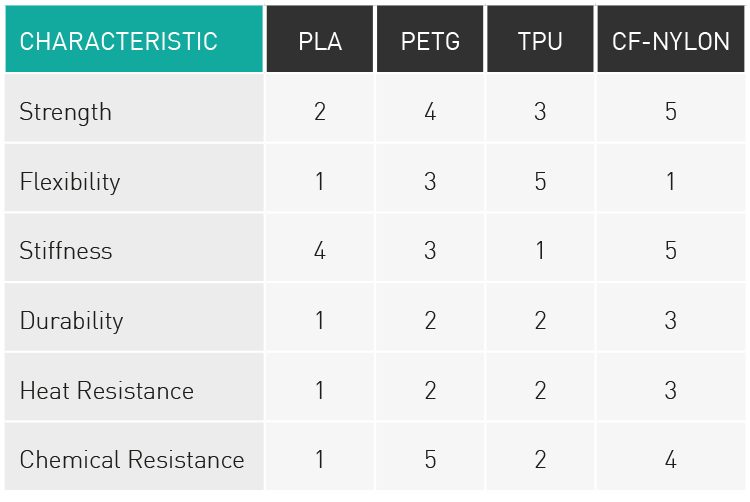
PETG
(PETG PART)
For printing PETG nozzle temperatures are between 240°C and 260°C, bed temperatures are around 90°c.
PET (Polyethylene Terephthalate) is a durable filament with good strength, when combined with glycol to produce PETG, the durability of the extruded material is increased. PETG can be classed as an engineering grade plastic used for structural applications due to its medium strength properties. PET/PETG has very good chemical resistance and It’s already used on thin water bottles, this allows it to be very good for food and medical grade parts and applications. PETG is less brittle than PLA, meaning thin sections won’t easily break when a load is applied, giving the overall part some flexibility. PETG is odourless and produces no toxic fumes when printed. Like PLA, PETG has little to no shrinkage when printing due to its excellent layer adhesion. PETG is a material that can be classed as a middle ground between PLA and TPU, with its higher strength PLA but its added flexibility of TPU. PETG filament also is available in clear and therefore transparent components can be printed.
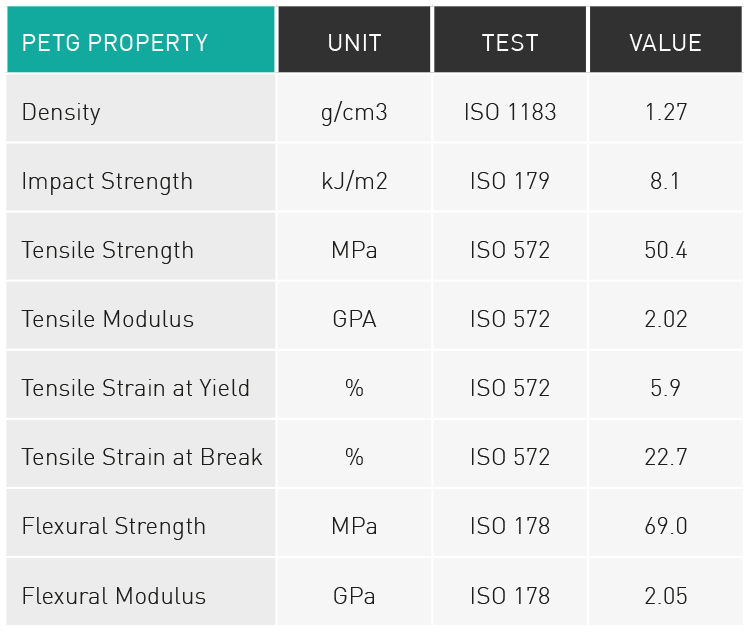
PLA
(PLA PART)
For printing PLA, nozzle temperatures are between 190°C and 210°C, bed temperatures are around 45°c.
PLA (Polylactic Acid) is the most commonly used filament in 3D printing. Although not useful for all industrial applications it is most suitable for rapid prototyping. PLA has a low glass transition point, it also has low strength and low durability. However it’s low cost making it suitable for quick iterative design development. PLA is the easiest material to print with, with it’s low printing temperature combined with no blobs and stringing during printing allowing for good quality prints. PLA produces the baseline for what can be 3D printed, if it can be printed in PLA, it can be replicated for other materials. PLA is a brittle 3D printing material, and considerations need to be taken for wall thicknesses and small detailing, however with PLA there is minimal warping and shrinkage providing consistent dimensional accuracy. PLA is classed as a non engineering plastic or standard material and should be used in non structural and non critical prototypes and end products. PLA is not toxic and doesn’t release any fumes when printed with, the end product does not emit any odours.

CF NYLON
(CF Nylon PART)
For printing CF Nylon, nozzle temperatures are between 270°C and 280°C, bed temperatures are around 70°c.
CF Nylon (Carbon Filled Nylon) is a composite engineering grade material, specifically used for structural and critical applications. CF Nylon has more strength than PLA, PETG, Nylon and TPU, with it also being very durable. Regular Nylon has high strength but also has a lot of flexibility like TPU. CF Nylon is different from regular Nylon because it is a blend of chopped Carbon Fibers within the Nylon. The blend of Carbon Fibers to Nylon is about 20% - 80% which removes the flexibility of Nylon and increases the overall strength. The overall finish of CF Nylon is more abrasive compared to PLA or PETG, a hardened nozzle is required to print with this filament due to its abrasive nature. Most CF Nylon components can be used within aerospace and automotive industries, however CF Nylon components can be used for JIGs. It’s low density means that a CF Nylon part can be a lightweight substitute for a metal component. Printing CF Nylon must be done at a higher temperature, with matching ambient temperatures to prevent warping and shrinkage on the print bed. CF Nylon is one of the strongest engineering filaments within the engineering grade category, before being compared with advanced engineering filaments such as PEEK and PEI. Just like Nylon, CF Nylon is hygroscopic and therefore requires special storage within a drybox, the amount of moisture within the filament will affect the surface quality and overall print quality, however once a part is printed, moisture does not affect the shape and quality of the printed components. CF Nylon is mostly found in black and therefore a post finishing painting process will be required for other colours.

TPU
(TPU PART)
For printing TPU, nozzle temperatures are between 220°C and 230°C, bed temperatures are around 50°c.
TPU (Thermoplastic Polyurethane) is utilised less within 3D printing, it’s primary characteristic is that it is flexible and printed components will flex. TPU is picked specifically for its characteristics in products such as elasticity, resistance to abrasion and wear. TPU is used within end products such as power tools, medical devices and caster wheels. The parts can be 3D printed and then used in combination with another material, such as a hand grip cover for a power tool handle. Clever design with TPU can allow for wrapping around existing products as the material can flex and fit over a part. TPU is available in several colours. TPU printed parts have medium strength, it is not as strong as a high performance material such as CF Nylon but is as strong as PETG. TPU prints a lot slower than other materials due it’s elastic nature and difficulty pushing filament through the nozzle, the thermoplastic part of TPU allows it to be printed from a 3D printer. The amount of flexibility within an endpart will depend on the print settings, for example changing wall thickness, layer height and infill percentage will all affect the end result. Increasing the wall thickness, layer height and infill will reduce the amount of flex within the design but will increase strength.

ความคิดเห็น